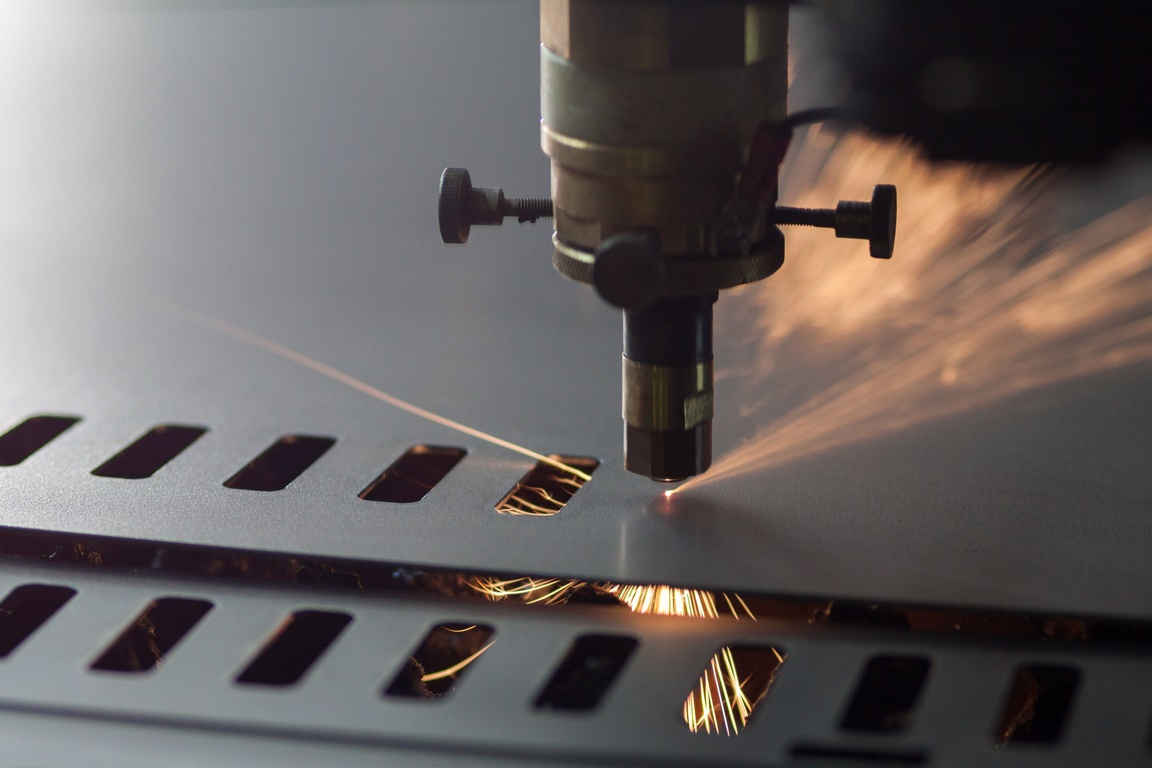
La maintenance industrielle est un domaine particulièrement vaste, qui englobe de nombreux corps de métiers. Elle a pour but de garantir la disponibilité des équipements de production industrielle tout en améliorant la durée de vie de ces divers équipements ainsi que la qualité du produit fini. Le tout, en respectant les règles en matière d’hygiène et de sécurité. Le but d’un technicien de maintenance industrielle est d’éviter une panne et donc, l’arrêt de la production industrielle. La difficulté principale réside évidemment dans la maîtrise des coûts. En effet, le moindre dysfonctionnement sur la chaîne de production pourrait entraîner des coûts supplémentaires. Mais alors de quelle façon une entreprise peut-elle diminuer les coûts de maintenance industrielle ?
Définir le coût de la maintenance industrielle
Maîtriser ses coûts de maintenance industrielle nécessite d’avoir des outils de gestion permettant de définir les coûts de base de la maintenance. À savoir, ce que coûte la main d’œuvre, les achats de fournitures, ou encore les contrats de maintenance. Pour mesurer ces coûts, il convient de prendre en compte plusieurs critères, comme les TRS (Taux de Rendement Synthétique), les coûts de fabrication produit, la valeur du produit neuf, les effectifs composants la maintenance ou encore les heures d’intervention. Autant d’éléments qui permettront de définir un coût pour pouvoir ensuite mieux le maîtriser.
Apprendre à détecter les dysfonctionnements
Plusieurs méthodes permettent d’organiser la production et la gestion des stocks tout en maintenant la qualité de sa production et en optimisant les coûts. Pour cela, il convient de commencer par anticiper les risques et limiter les dysfonctionnements lors du circuit de production. Cela peut être lié à l’interruption des machines, à un rendement insuffisamment élevé, aux pertes de matières, à des retards de livraison ou encore à un défaut de qualité sur le produit. Analyser ces dysfonctionnements permettra de connaître les causes des pertes et de les éviter à l’avenir. Repenser son organisation induira nécessairement une réduction des contrôles et une meilleure gestion des délais de livraison : un client livré à temps est un client satisfait.
Revoir la philosophie de l’entreprise à la Kaizen
Toute la philosophie de l’entreprise peut être repensée dans le cadre d’une démarche de réduction des coûts. On peut alors faire référence au processus d’amélioration continue, aussi appelé « lean ». Il s’agit d’un effort continu visant à améliorer les process, la qualité des produits et/ou des services fournis. Plus concrètement, l’entreprise ne doit pas visualiser le problème comme un échec, mais plutôt comme une opportunité de s’améliorer. Un processus qui implique d’être prêt à remettre toute une organisation en question en gardant à l’esprit que l’amélioration est infinie. Une culture d’entreprise inspirée du Kaizen, un style de management japonais : « kai » = changement et « zen » = bon.
La méthode du Kanban ou une production à flux tendus
Les japonais ont manifestement beaucoup à nous apprendre en la matière. En effet, la méthode du Kanban est une autre façon de gérer ses stocks et qui consiste à appliquer un système de production à flux tendus. En clair, un traitement « juste-à-temps » de la demande clientèle. On ne produit pas plus que la demande, ce qui implique d’avoir une équipe de production et des fournisseurs réactifs. Cette technique permet de réduire les coûts production, de stockage et de délais (fabrication et livraison).
Une pensée sur “Plusieurs méthodes pour réduire le coût de la maintenance industrielle”